“Recycling is coming”: mineral industry gears up for supply chain evolution
Mineral Recycling Forum 2022 Dubrovnik Review | 2023? same place, same time!
If we were to talk about high drama in Dubrovnik, you would be forgiven for immediately thinking of the successful medieval fantasy TV drama series Game of Thrones, much of which was filmed in and around the beautiful old town of Dubrovnik.
However, those attending IMFORMED’s Mineral Recycling Forum 2022 on 28-30 March, were witness to quite another drama unfolding: very much of this time and within the refractory recycling sector, as competing players squared up against each other, and those caught in the middle made their opinions heard – “Game of Refractory Recycling” perhaps?
In all seriousness, the excellent presentations, ensuing lively debate, and passionate discourse among networking delegates not only made for a superb conference, but was also indicative of just where the mineral recycling industry stands at present.
Whether recycling refractories, slags, ash, mine tailings, or other industrial waste, it seems that apart from the few well-established pioneers in this business, many companies are still trying to get to grips with just how to go forward with a recycling strategy.
Whether to invest in an in-house business/plant? Partner with an independent recycler? Join forces with same-sector players? How much and how far to invest? And crucially, what impact will it have on customers and markets?
These and other key topics were under the spotlight in Dubrovnik earlier this year, and will again be centre stage next year at IMFORMED’s Mineral Recycling Forum 2023, at the Hilton Imperial Dubrovnik, 28-30 March 2023 – Book now for Early Bird Rates & Call for Papers! (full details here).
The bottom-line is that mineral recycling is coming, and as a mainstream activity, and not as a somewhat esoteric sideshow, as has often been previously perceived.
How the industry goes about developing a coherent structure and strategy for this evolving supply chain option is of primary importance, continuing challenge, and frankly, a necessity which cannot wait for much longer.
Don’t miss out, book now!
Call for Papers | Full Details Here
What delegates said about Mineral Recycling Forum 2022:
Well organised, excellent programme. A huge networking opportunity and awareness of challenges and market trends.
Shirshah Amerkhail, Sustainability Advisor, IMA-Europe, BelgiumExcellent talks and great venue, well organised.
Nancy Easterbrook, Director Recycled Minerals, HarbisonWalker International, USAI’d like to compliment you with this successful conference. I was pleasantly surprised with the quality of speakers, as well as the attendance.
Alex Medendorp, Sales & Marketing Director, Nedmag, NetherlandsLots of information. Excellent, best one yet.
Mark Connor, Director, Richmond Reclamation, UK
Here are the presentations reviewed from this year’s conference.
A new era of accelerated recycling
Mike O’Driscoll Director, IMFORMED, UK
Setting the scene in his introduction, O’Driscoll observed a new era of mineral exploration, sourcing, development AND recycling in the industrial mineral business.
An inevitable development, both spotlighted and advanced by the recent pandemic and tragic Russia-Ukraine war, has prompted an industrial mineral sourcing strategy rethink, and at the same has accelerated mineral recycling activity and planning.
Primary drivers are summarised as a “Rule of Six”:
- Environment: saving the environment, drive for the “Circular Economy” gathering momentum
- Limited primary sources: shortage of commercially developed “critical” mineral resources and processing plants
- Source overreliance: risky overreliance on supply/trade from limited overseas sources
- China in change: supply issues, range of factors.
- Emergence of hi-tech growth markets: to become mainstream, particularly in the energy sector (eg. Li-ion batteries, EVs, solar, wind), and thus demand for respective critical minerals (eg. lithium, graphite, rare earths).
- Recycling technology more economic/established: from esoteric, expensive sideshow, to mainstream processing line; opportunities sensed and sought after
In conclusion, the main general trends going forward for the industry will be:
- More primary mineral producers (miners) involved in recycling tailings and other waste sources to offer wider product range (including blends?), providing a favourable “green” label on portfolio (same goes for mineral consumers).
- “New normal”: Recycled raw materials will become a “normal” supply chain option for mineral buyers
- Government input: expect more of it, eg. Critical Mineral policies; recycling initiatives, eg. Feb. 2022: US Dep. of Energy $6bn grant for batteries; 50% earmarked domestic supply plus recycling.
- Challenges remain: eg. competitive pricing; grade quality; advanced sorting techniques; development and investment processing technology.; harmonisation of waste handling/permitting; “education” of industry and ridding of stigma of recycled material as “contaminated” and “secondary”
- Opportunities: for companies to process minerals from waste, develop and supply sorting technology and equipment
- New mutually beneficial alliances: increasing between waste sources (mineral end users) + recyclers, new logistic chains evolving
- Supply chain co-operation: closer and essential, eg. to enable above, and in modifying end product formulations to ease end-of-life recyclability
Recycling minerals at Imerys
Frédéric Jouffret, VP Global Science & Technology, France & Richard Tamblyn, Senior Process Innovation Manager, UK
Jouffret outlined Imerys’ sustainability programme, SustainAgility, which was launched in 2018, comprising six pillars structured into three key areas (see chart).
Imerys’ objective is to proactively steer the overall product and project portfolios towards improved sustainability performance and sustainable solutions, with two specific goals in mind: assess 40% of portfolio against sustainability criteria by 2022, and with 50% of New Product Developments scored as “Sustainable solution”.
“Circular minerals” for Imerys is any activity that breaks the traditional linear business model where virgin materials are processed and sold.
This can include:
- Extraction from Imerys historic by-products (pre-consumer)
- By-products from our customers, or from other industries (post-industrial)
- Recycled minerals from end users (post-consumer)
- Supporting external circular value chains with our mineral solutions
Examples of Imerys developments include the Imerloop-F range of products based on recycled material from the paper and board industry, where there are significant CO2 reductions possible.
Jouffret acknowledged ongoing challenges in such recycling activities, including: dealing with impurities, managing quality parameters, and regulatory issues.
Optimisation of mineral flows: matching the policy and business perspectives
Shirshah Amerkhail, Sustainability Advisor, IMA-Europe, Belgium
Amerkhail described IMA-Europe in a nutshell, minerals and their applications, circularity, relevant policies, and business models, tools, bottlenecks, and opportunities, and take away messages.
The EC’s new circular economy action plan objectives and measures were outlined, comprising three main pillars: to reduce EU consumption footprint; double the EU circular materials use in the next decade; and transition in a way to boost the economy.
A focus was given on waste shipments within the EU, with some 70m tonnes circulated each year. The Action Plan includes modernising EU Waste Law, with an objective to ensure that the EU does not export its waste challenges to third countries.
Amerkhail demonstrated that there has been an increase in the recycling rate of minerals in the EU, and went on to explain business models contributing to the Circular Economy and tools that can help in assessing circularity.
Despite the high recycling rates, the EU still needs around 200m tpa of minerals, and there is a need for close industrial co-operation to exchange best practices and make industrial symbiosis operational.
Brine recycling: Salts Plus
Stefan Schlag, formerly Director Inorganic Chemicals & Minerals, S&P Global Commodity Insights, Switzerland (now Owner, Salt Market Information)
Schlag started by questioning the reasons to recycle salt, which included no lack of reserves and resources, and aspects of the economy, followed by an examination of several examples of salt recycling from industrial waste water, drilling mud, desalination plants, salt disposal, and fly ash.
In most cases salt is recycled from waste brines, from which impurities need to be removed. Evaporation of water and concentration to crystallisation point is costly, and compares to similar if not more of the cost of production of vacuum salt.
In essence, the reasons to recycle salt are “beyond economy and resources”. They include:
- Circular economy claim/marketing
- Missing permits to dispose of brines or to pile-up salt
- Cost of disposal of wastewater
- Volumes of wastewater and composition exceeding capacity of municipal wastewater plants
- Water scarcity/recycling of industrial waste water/zero waste approach
- Water scarcity/desalination/ recycling of salt from reject to protect the environment
Brine recycling in the industry, particularly in chloralkali electrolysis, is economically more advantageous especially when disposal of brines is environmentally unsustainable and cost of sustainable disposal is elevated.
Water scarcity is the main driver of salt recycling projects, involving desalination and recycling from rejects, protection of groundwater, and re-use of water.
Li-ion battery market and its mineral recycling future
Robert Colbourn, Publisher, Benchmark Mineral Intelligence, UK
Although unable to attend owing to Covid-19, Colbourn kindly delivered his fine presentation to the conference remotely online.
The lithium ion supply chain from raw material to application was explained followed by the soaring demand growth for electric vehicles using LIB. Battery manufacturing capacity expansions have accelerated with over $150bn of investment commitments in 2021, some 282 gigafactories were in the pipeline at the time of the conference.
Colbourn explained how both lithium and cobalt output would struggle to keep pace with demand growth rates in LIB of 20-25% CAGR.Also, battery raw material costs have increased since the onset of the pandemic.
Key points for LIB recycling were described as:
- Lithium ion’s raw material disconnect
- Price rises have improved economics
- Regulation & policy; ESG factors
- Cathode vs anode materials; recycling process
- Scrap vs end of life
LIB recycling feedstock will be dominated by battery plant production scrap in the near term, and Colbourn considered that even with recycled supply, lithium demand faces a long term shortfall.
Bauxite tailings valorisation: From test works to industrial scale up
Thomas Baumann, Sales & Business Development Manager, AKW Apparate + Verfahren GmbH, Germany
Baumann’s presentation looked at bauxite tailings valorisation and covered bauxite ore in general, a case study of a West Africa bauxite mine, and a conclusion with AKW’s equipment and process design capabilities.
After summarising bauxite processing, and its generation of bauxite residue as waste, Baumann underlined that to identify potential recycling possibilities, and to evaluate realistic recovery rates of valuable bauxite qualities, extensive test procedures are necessary to get reliable results and define serious performance targets.
A comprehensive test programme in the technical laboratory of AKW Equipment + Process Design was outlined regarding a West African bauxite operation generating 200 tph <2.4 mm tailings.
This resulted in development of new bauxite tailing treatment units which delivered significant recycling rates of 50% for both fresh and existing bauxite tailings, for the former, this results in longer lifetime of the deposit and reduces the discharge of tailings.
Challenges for the slag value chain in Europe
Thomas Reiche, Chairman, Euroslag, & Managing Director, FEhS-Institut für Baustoff-Forschung eV, Germany
Reiche started by explaining why slag-based construction materials and fertilisers are best practice examples for the circular economy and the preservation of natural resources.
Ferrous slag has already been successfully used in various applications for a long time and is at a high level in Europe. In 2020, total European ferrous slag production was 39m tonnes (21.8m tonnes BFS, 17.1m tonnes SFS).
Reiche reminded that the EU has set very ambitious CO2 reduction targets, which require a fundamental transformation process especially for the integrated route of steelmaking.
The upshot is that the “slag mix“ will be substantially different in the future, and along these lines:
- Decrease in Blast Furnace Slag (GBS/ABS) and Basic Oxygen Furnace Slag (BOF) despite high GBS demand by the cement industry
- Increase in Electric Arc Furnace Slag (EAF)
- CO2 reduction targets
- General shift towards scrap as raw material
- “New slag types” due to new iron and steel making processes (direct reduction, different slag types in the EAF)
- R&D required to secure utilisation of these slags
R&D will need to focus on to what extent these new slags compare to the previous slag types. Research on the conditioning of EAF slag has been ongoing for several years. Reiche said the aim is to work on “GBS 2.0“ from both scrap-based and DRI-based EAF slag.
As well as increasing relevant R&D, Reiche underlined that there was a significant need to improve framework conditions and specific legislation, including revision of the European Public Procurement Directive.
He cited the “battle” over the framework conditions for the use of secondary raw materials as fertilisers under the scope of the European Fertilizers Regulation as the “worst” example of the discrepancy between theory and practice in the circular economy.
Insights into recycling of metallurgical slags, bricks & dust
Dr Jan Lampke, Head of Sales & Projects, Haver Engineering GmbH, Germany
Using working examples of minerals and fertilisers, Lampke explained how mining and metallurgical know-how can be applied in the screening, pelletising, and development of complex plants, to enable recycling of slags, bricks, and dust.
Among the examples was a description of a screening and crushing plant for crushed bucket excavated material from 500 mm to 0 to 2 mm, the feedstock material was slag from ladle cleaning and magnesite brick.
The requirements called for a plant in limited space (length 40 m, width 9 m, height 15 m), high maintenance and access requirements with fire protection claim, reduction of dust and noise emissions (dedusting system and soundproof housing), high expectation of E/I&C technology (electronic instrumentation and control), and high requirement for corrosion protection class C4.
Day 2 focused on refractory recycling trends and developments. By then the conference had gained a somewhat febrile atmosphere owing to the announcement on the eve of the event that RHI Magnesita had upped its game in the sector with a joint venture with Horn & Co. Group, called Horn & Co. RHIM Minerals Recovery GmbH (this was reinforced on 15 November with the launch of MIRECO, the new brand and recycling platform of RHI Magnesita and Horn & Co Group).
Sustainable refractory concepts
Dr Helge Jansen, Managing Director, Refratechnik Steel, Germany
Jansen kicked off the session with an excellent paper covering the situation of MgO-C production in Europe today, the fateful dependence on Chinese products, the carbon footprint of MgO-C bricks, features of alternative MgO raw materials, and sustainable refractory concepts in Europe.
He outlined the increasing challenges and pressures facing refractory raw material consumers in recent years and considered targets for a new approach to include:
- Reducing the dependence on China
- Reducing the carbon footprint of our MgO-C production
- Increasing the availability of European refractories for European steel plants
To help in reducing the dependence on China and lower the carbon footprint of MgO-C production, complete recycling loops of MgO C with short supply chains should be enabled.
MgO-C “regenerates” are an important raw material source for MgO-C bricks, although due care must be taken to minimise impurities and maintain high quality material.
Jansen introduced Refratechnik’s “New Approach for Europe” using high performance raw material concepts with higher portions of recycled MgO-C bricks used in combination with high quality dead burned magnesia and fused magnesia from the group’s captive producer QMAG in Australia.
“In this unique combination the use of recycled MgO-C can be increased in comparison to today‘s standards for ladle and EAF linings. At least 25% of fresh MgO will be replaced by recycled material.” said Jansen. “This results in new possibilities for technically and ecologically forward looking and cost effective concepts ‘Made in Europe’”.
It was demonstrated that replacement of 25% primary MgO by recycled MgO-C leads to substantial savings of CO2, of almost 8,000 tpa.
Refratechnik has started a recycling JV in an existing MgO-C plant for ladle and EAF bricks in central Germany, and will expand in two steps: 20,000 tpa in 2022, and 40,000 tpa in 2026.
Closing the loop: refractories recycling
Sabrina Salmen, Senior Executive Recycling, RHI Magnesita, Netherlands
Salmen started with the question “Why are we here today?”, and highlighted a range of driving forces from the Paris Agreement to future EU Carbon Border Tax.
“It is RHI Magnesita’s target to reduce [CO2] emissions by 15% per tonne of finished goods by 2025.” said Salmen.
Salmen showed how other industries were evolving a circular economy from a linear business, such as cement, aluminium, steel, plastics, and food.
Although refractory recycling took place in the 1990s, little has evolved since, especially in technology for processing and cleaning. Salmen considered the yield remains low with many spent materials remain without application, and that from 2025 the recycling sector would be “Loading” with “a new generation of engineering through circular minerals required to enable the refractories CO2 neutrality.”
In developing new technologies for using spent refractories, RHI Magnesita is focusing on four Strategic Circular Economy Pillars: sourcing, processing, consuming, and refractory sales; supported by three main lines of research in: recycling characterisation and sorting; recycling stabilisation; and valorising low value waste material.
Salmen concluded with examples of RHI Magnesita’s successful recycling activity in the cement industry, and in sourcing and processing in China and Europe.
The presentation was followed by a lively Q&A session, where the recycling strategy of RHI Magnesita was questioned by certain delegates with a high degree of passion. Suggestions of RHI Magnesita having a “panic attack”, “missing the boat”, and questioning “where are you going?” made for an interesting debate, and were handled with dignity under fire by Salmen.
Restoring value to refractories
Bruno Dorier, Director, Valoref Saint-Gobain, France
Created in 1987, and a wholly-owned subsidiary of Saint-Gobain, Valoref was a pioneer in the management of refractory waste from glass furnaces.
Dorier went on to describe Valoref’s recycling services for refractory and ceramic waste and its recycled product range.
The company handles 35,000 tpa of refractory waste from 55 countries comprising zirconia, magnesia, alumina, and chrome-containing material. Ceramic waste is also processed, including abrasive wheels, silicon carbide, and sand blasting media.
Dorier underlined the importance of understanding issues related to the management of ceramic and refractory waste, which include environmental, legal and economic issues and expanded on the many reasons to use a Waste Manager/Recycler.
Valoref’s two main refractory waste management solutions were described: Valorwaste and Valorbox, the former removing refractory waste and the latter managing regular waste.
A circular economy solution in the field of steelmaking waste: ReStoRe technology
Massimo Proietti, Technical Director, Deref SpA, Italy
It was a welcome return to Mineral Recycling Forum for Deref, which had participated in our inaugural event in 2016 and have conducted much work since then.
Proietti explained the project ReStoRe (REfractory and STeel REcovery): technology associates dedicated equipment, organisation and slag engineering to create a complete and operational solution for steel exhausted refractories valorisation.
The main stages of metal pre-selection, primary sieving, metal separation, sorting, treatment, and storage and packaging were described.
Basic material, alumina and other reusable parts are separated and machined into required dimensions to be reused in secondary metallurgy instead of consumables such as lime and alumina flux.
From the first ReStoRe plant almost 150,000 tpa of waste from a range of steelmaking vessels is processed, yielding recycled dolomite and magnesite. The second plant processes 27,000 tpa waste yielding secondary raw materials for refractories.
Proietti also explained the dolomite/magnesite and bauxite cycles regarding their CO2 emissions with recycling using the ReStoRe concept.
The ReStoRe technology enables a significant reduction of CO2 emissions, as the primary production of consumables (ie. lime, dolime and bauxite flux) has a strong environmental impact owing to the high temperature calcination involved in their processing. In this way, the ReStoRe approach breaks with the linear model of resource consumption that follows a “take-make-dispose” pattern and changes it into a circular one.
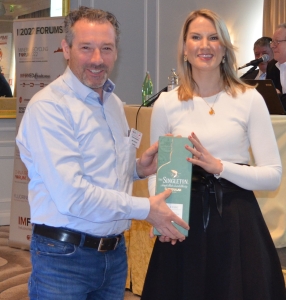
Winner of our Prize Draw Erwin Grossman, Mine Feuerfest, presented by Bettina Horn, Consultant.
Thank you and hope to see you again soon!
Mineral Recycling Forum 2022 was a most stimulating and enjoyable conference, not least that it was our first live event post-pandemic, and at a wonderful location (so much so, that with general agreement, we are returning in 2023!).
We are indebted to the support and participation of all our partners, speakers, and delegates for making Mineral Recycling Forum 2022 such a success, and ensuring a fruitful time was had by all.
We very much look forward to meeting you again, and with that in mind we have announced Mineral Recycling Forum 2023, at the Hilton Imperial Dubrovnik, 28-30 March 2023 – Book now for Early Bird Rates & Call for Papers! Full details here.
Registration, Sponsor & Exhibit enquiries: Ismene Clarke T: +44 (0)7905 771 494 ismene@imformed.com
Presentation & programme enquiries: Mike O’Driscoll T: +44 (0)7985 986255 mike@imformed.com
Free Mineral Recycling Forum 2022 Summary Slide Deck Download here
Missed attending the Forum? A full PDF set of presentations available for purchase.
Please contact Ismene Clarke T: +44 (0)7905 771 494 ismene@imformed.com